Cooperation does not end with finalising a warehouse installation. Also, and especially, after the handover, our clients can still count on us. Warehouses are often used intensively, forklift trucks and other vehicles go in and out. The materials we use are always of the highest quality, but wear and tear are inevitable. Moreover, heavy products are also often stored at height in warehouses. An installation must therefore be built in accordance with all current applicable standards. Safety comes first and acting proactively is the norm.
Inspections before and during commissioning of the warehouse installation
Inspections: a must
Once a new installation is in place, we give our customer an acceptance protocol in which we declare that everything was installed in accordance with the rules of good workmanship. In addition, if required, an inspection will be carried out before commissioning by an external certified body for technical control. So that nothing is left to chance, and to guarantee a definite quality, we will always recommend an inspection.
Periodic inspections during use
Shelving that is in constant use will obviously be more likely to get damaged. Therefore, interim monitoring and inspections are necessary. It is a guaranteed method to detect and resolve issues in a timely manner, and as a result to avoid unpleasant surprises.
How is an inspection performed?
Interim inspections are carried out periodically, depending on the intensity of use. First, the existing shelving structure is mapped out. After the site visit, an inspection report is drawn up with observations, recommendations and motivations to repair or replace faulty components. The day-to-day operations are not disturbed.
The inspection report
After the inspection, all recommendations are listed in an inspection report, consisting of an overview and a detailed list. The overview lists which materials should be replaced per make; the detailed list indicates in which areas action should be taken. Once the repairs and replacements have been completed, a new inspection will be carried out if necessary.
Loading notices
During an inspection, the carrying capacity of each rack is established. The main focus points and the maximum carrying capacity of the rack are marked on the rack itself as a guideline for the person who puts products on the rack or removes them. These carrying capacity tags must be present on each installation. If not, the organisation carrying out the inspection can install these tags.
What do Hardy’s Industries do?
The inspection itself is carried out by an external body.
If desired, we can take care of organising the inspection.
After each inspection, an inspection report is drawn up, listing in detail what needs to be done to make the shelving compliant and safe before or during use. We follow the guidelines of this report scrupulously and, in consultation with the client, we take care of all necessary repairs and/or replacements.
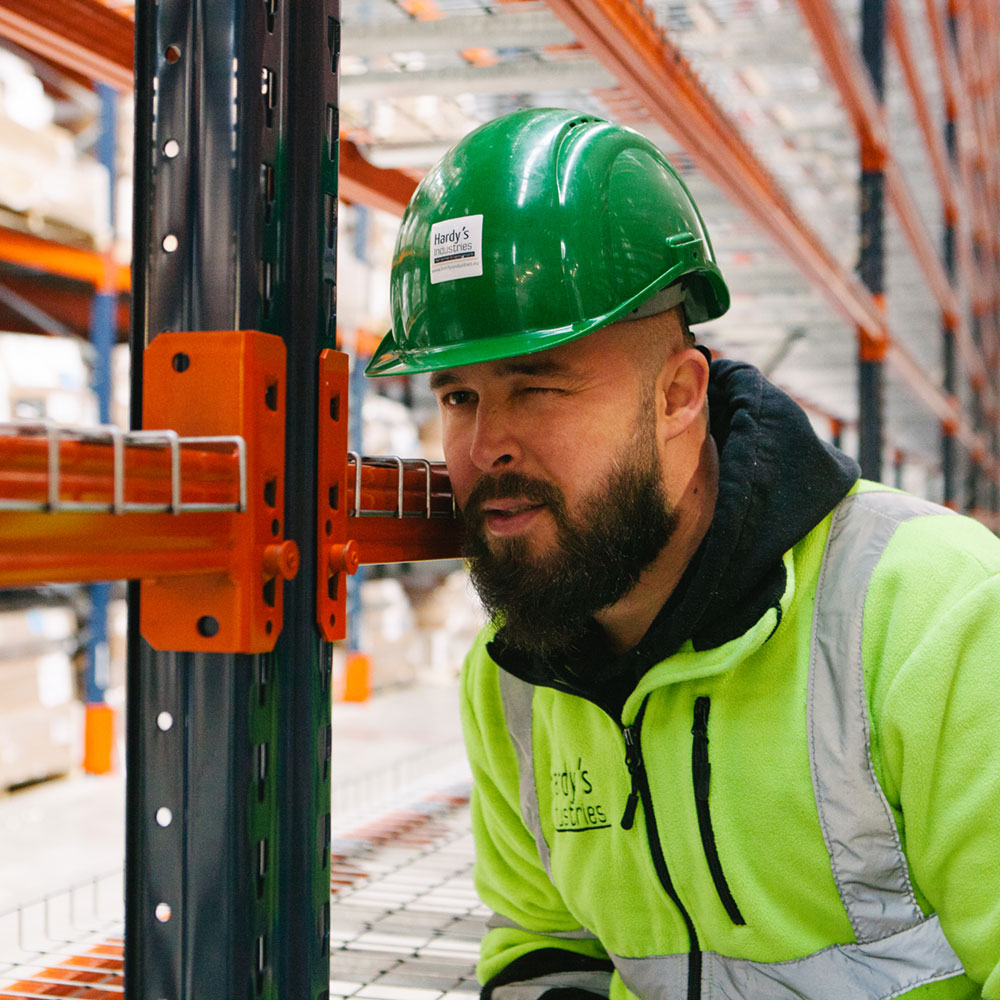